Pretty much everyone in manufacturing by now at least has heard about Industry 4.0 and Industrial IoT. While many are in the first stages of industrial transformation, the more mature goals of open data ecosystems of value/collaboration and customer-oriented innovation in manufacturing for now mainly remain intentions.
As mentioned in our Industry 4.0 overview there are significant similarities regarding digital transformation maturity and Industry 4.0 maturity.
This of course isn’t surprising. Manufacturers and other companies in the broader scope of the Industrial Internet, digital transformation of manufacturing and anything related with it share several common challenges and issues as other organizations going through digital transformation.
Also in the initial stages of Industry 4.0 maturity it’s mainly about internal goals: higher productivity, saving costs, testing the waters with low-hanging fruit types of goals with immediate returns and ‘easy’ IoT use cases, enhanced automation and so on. True innovation in manufacturing based upon interoperable and open ecosystems with an end-to-end data approach and a focus on the end customer and consumer is rare if existing at all.
Increasing innovation in manufacturing through new technologies, process and business models requires a consistent data approach, higher flexibility and a focus on stakeholder and partner ecosystems of value with the customer – and customer of the customer – taking center stage
In digital transformation in the broader sense there is more focus on customer-facing goals in some areas and in some sectors for all the obvious reasons such as the type of process, the ways to achieve a specific goal, the degree of contact/interaction with the (end) customer and/or the role of the consumer in the digital innovations and business as such (think the automotive industry and the role of technology in the driver experience and in the branding of car manufacturers where ‘tech’ is omnipresent).
In some industrial markets such as oil and gas or mining the focus is of course less on consumers. And in manufacturing, the original scope of Industry 4.0, it really depends on what is manufactured for whom and the level of Industry 4.0 maturity. Think about the mentioned example of car manufacturers versus, let’s say, airport baggage conveyor and carousel part manufacturers (OK, we stretch it a bit): quite different markets indeed, yet both manufacturing.
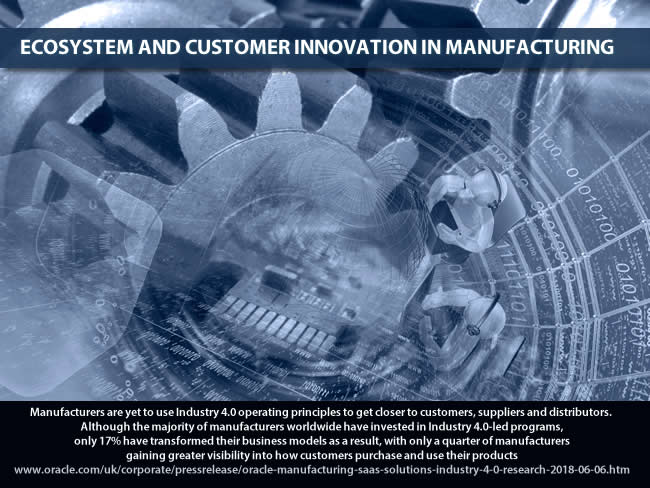
The traditional areas of innovation in manufacturing and Industry 4.0 with the customer in mind
Other manufacturing companies having relatively strong ties with consumers in different ways and/or innovate with the end customer in mind.
These include, among others, manufacturers of fast moving consumer goods (FMCG, the word consumer is in it), pharmaceutical companies (loads of patient data and analysis of clinical trials on the R&D side, a focus on customer experience innovation since ages, direct-to-consumer marketing, certainly in consumer drugs, etc.) and of course consumer electronics and tech where, increasingly, data on behavior and usage of the devices and the applications are leveraged (not always in the most ethical ways as we all know) and where in several categories IoT has made or is making its entrance with Consumer IoT spending globally poised to rank fourth in 2018.
As far as innovation in manufacturing is concerned we could say that mainly automotive, tech, pharma and some areas of FMCG indeed also innovate with the consumer involved and/or targeted one way or the other. However, this was already the case in several areas before anyone even used the term Industry 4.0.
Overall, organizations that are further in their Industry 4.0 roadmap leverage data, IoT (with IoT in manufacturing still the main IoT spending category), artificial intelligence and industry-specific technologies to offer new services to their customers and where possible to consumers.
Just over a third of manufacturers have used Industry 4.0 technology to remove all data silos from across their value chain, while only 40% have an open exchange of data with suppliers and distributors. For decision making processes, less than half, have integrated customer data and just 45% have integrated supplier and distributor data (Oracle, June 2018)
In the as-a-service economy, as it also shows in Industry 4.0, typical examples include better and advanced monitoring and predictive maintenance services, advanced and predictive analytics enabling even more new services, digital twins to understand product usage by end customers to improve products (and design new ones), IoT and AI applications to offer higher levels of comfort in, for example, facility optimization and so on. These areas indeed are customer-oriented forms of innovation in manufacturing and/or in industrial segments.
Yet, all in all it’s still early days for most customer/consumer-oriented, customer/consumer-facing and consumer-involving initiatives and innovation in manufacturing, just as it is for most organizations in digital transformation and for many in the scope of IoT projects. This is even more so for the more mature goals of Industry 4.0 where the customer by definition is key.
It shouldn’t indeed be forgotten that Industry 4.0 is a documented and very data-intensive vision with reference architectures and models enabling (initially) the manufacturing industry to, in the end, innovate, change business models, shorten the journey from design and production to actual ‘consumption’ and usage, here and there skip some intermediaries in doing so or at least significantly speed up the process with, in the end, the customer and consumer in mind and novel ways to directly engage with the customer, for instance by offering highly personalized products through new channels and models.
The degree in which this happens or can happen depends on the context, the organization, its leadership, regional differences, you name it. Even if we stick to manufacturing it’s clear that one manufacturer is far from the other, just looking at the various types of produced goods and end customers as we just did.
Challenges slowing down the journey to ecosystems of value, collaboration and innovation in manufacturing and Industry 4.0
Moreover, there is no ‘universal’ Industry 4.0, industrial transformation or digital transformation approach that fits best. Each business is different, has different customers and operates in different circumstances (whereby Industry 4.0 is used as an umbrella term making it key to look at “general” Industry 4.0 predictions and advice with caution).
Industrial companies obviously share ample challenges with others too, albeit sometimes in inherently different ways:
- Country-specific or regional and industry-specific regulatory frameworks and changes.
- Various economical and geo-political challenges which especially in recent years have increased with traditional trade partnerships and alliances under pressure.
- The presence of legacy systems and requests to fix those to solve short-term challenges as the pressure to attain business goals in the here and now is high.
- Challenges regarding the definition of an Industry 4.0 or simply digital transformation strategy in the industrial context with the proper guidance and needed buy-in.
- An overload of new technologies and offerings with vendors often moving way faster than manufacturers and not focusing enough on what really matters for clear benefits of organizations and their customers.
- Having to deal with ample demands on all fronts at the same time and often coming from teams that de facto still operate in silos: process automation (with robotic process automation as the hot topic of the day in business process automation), the front-end and customer-facing side of the business, the demands from management, the need to converge IT and OT (which isn’t just about technologies but most of all about people, culture, skills, collaboration, processes, etc.).
- Too much focus on reaping short-term goals alone with internal goals and cutting costs (also regarding labor) being very tempting for many executives and coming with the risk of remaining stuck in the early stages of industrial transformation.
- Challenges on the level of getting basics right with siloed and unused data sources, too much paper, resistance to change, digital security and cyber resilience woes (that need to be tackled) and so forth.
- A lack of focus on the human element, both in the industrial transformation journey and the goals of Industry 4.0 projects, with on top challenges to find the right people with the required skills in the first part of the equation.
- The eternal challenge of not being able to fully leverage data, let alone of implementing the end-to-end data vision which Industry 4.0’s reference architecture model (RAMI 4.0) in the end boils down to: from the life cycle and value stream dimension to horizonal and even vertical integration.
- A specific challenge in the brave new world of IoT and of Industry 4.0: a lack of standardization, interoperability and regulations with far too many standards, protocols and even players on all levels of the IoT technology stack.
- Challenges regarding organizational culture, vision, redefinition of processes and how to develop new business models, let alone changing existing ones.
Moving from enhanced productivity and higher flexibility to capabilities of innovation in manufacturing
This list is far from complete but does give some of the reasons why Industry 4.0 today is more hyped than deployed in a relatively mature way, let’s face it.
For those who are active in ‘the market’ of Industry 4.0 solutions, whether it concerns industrial software such as manufacturing execution systems, robots and cobots or the essence of cyber-physical systems, the IoT and the related technologies/architectures to unlock the value of IoT (e.g. artificial intelligence, fog computing and edge computing), all of this might seem like nonsense and industrial transformation goes faster than we claim or Industry 4.0 maybe even isn’t hyped at all.
We do realize that some organizations are far ahead, that the market is evolving fast, that there are great projects and that organizations across the globe are on a journey of offering new services, enhanced efficiency and more mature goals whereby everyone must start somewhere.
It’s good to see manufacturers reaping some rewards from their Industry 4.0-led programs, but there’s clearly a long way to go before their investments begin to have the disruptive and transformative impact they promise. Removing siloes internally is a good start but that digital thread has yet to extend outside the organization and throughout the value chain (John Barcus, Vice President, Manufacturing Industries at Oracle)
We also know that some governments and alliances of different kinds are pushing the agenda. But for those more advanced goals with the customer/consumer and innovative capabilities on that level it simply is still far too soon, not considering those manufacturing segments closest to consumers.
Still, for many it is just beginning where limited goals are set and benefits achieved.
It isn’t the first time we emphasize that enhanced productivity is just the beginning and that in next stages increased flexibility, quality and speed come in the picture as the Boston Consulting Group (BCG) also stated end 2016 as BCG’s SlideShare presentation regarding Industry 4.0 for US manufacturing shows.
However, it needs to be re-emphasized now and then since the risks of remaining stuck in the first stages where it is all about enhancing productivity (and saving costs or automating ever more with “cost efficiencies” as the sole goal) are real and can lead to missing then true benefits and value of Industry 4.0 or, worse, become irrelevant and lose any competitive advantage.
The fact that precisely 1.5 years after the BCG presentation emphasized this and in June 2018 international research commissioned by Oracle shows that the focus of Industry 4.0 is on internal changes rather than on the removal of supplier, distributor and customer silos says enough.
The research is all the more interesting as it isn’t focused on the US but on the main Industry 4.0 countries in the EU (the UK where manufacturers also in June warned that Brexit slows things down and March manufacturing figures showed a slump in manufacturing output, France, Germany and The Netherlands), in Switzerland, in the UAE and, particularly interesting in a global scope, in China.
It shows that in the surveyed countries manufacturers don’t leverage essential Industry 4.0 principles (in the real sense of “Industrie 4.0”, not the buzzword) such as mutual interoperability, transparency and decentralization to get closer to customers, suppliers and distributors.
Removing data silos, having open data exchanges with partners and integration customer data on the road to mature innovation in manufacturing
Of the 700 surveyed manufacturing executives only one third so far used Industry 4.0 technologies to put an end to data silos within the end-to-end value chain and 40 percent have an open data exchange with suppliers and distributors. Moreover, less than half integrated customer data, and only 45 percent integrated supplier and distributor data for decision processes.
Finally, so far only 17 percent have adjusted their business model and only a quarter have gained more insight into how customers purchase and use their products with just over half using customer data as input for designing and creating new products (a typical digital twin technology use case).
While all in all these numbers, taking into account what we mentioned, might seem not bad at all, do note that respondents were from organizations in the fields of automotive, high tech, textiles, FMCG and pharma and chemicals (indeed, industries where quite a lot is happening and/or the consumer is already present, including some we mentioned and high tech where, well, there is quite some tech and customer data going on) and that there is often a gap between what executives say (it also isn’t clear how and to what extent manufacturers, for example leverage end user and customer data) and reality in the field. Respondents are from organizations with at least 250 employees, yet we don’t know the precise details so it’s possible that mainly large companies responded.
This doesn’t mean that we doubt the good intentions of Oracle but we’re pretty sure that if you look on a broader scale and at several levels in practice the actual numbers in some of the areas Oracle looked at really are still significantly lower.
Anyway, the good news is that, according to the survey, “when it came to next steps for their Industry 4.0 implementations, manufacturers ranked customer-facing operations as the most crucial place for change within the next three years and half said they would be focusing on removing data silos while 47% acknowledged they needed to create a more open exchange of data with suppliers and distributors”.
Between intent, plans and acknowledgement and reality in the future of course are many challenges and changes – so hopefully within the next three years and a half we’ll indeed see more of the “true” open data and customer-facing expectations and plans turned into reality.
More findings and links in Oracle’s press release: “Customer Connection Missing as Manufacturers Yet to Produce Rewards From Industry 4.0”.
Top image: Shutterstock – Copyright: archerix – All other images are the property of their respective mentioned owners.