Digital twins are poised to transform manufacturing processes and offer new ways to reduce costs, monitor assets, optimize maintenance, reduce downtime and enable the creation of connected products.
The digital twin model, although not new, is entering manufacturing and other industries such as the construction industry fast. IoT is one of the drivers. Digital twins in an industrial, non-academical, context.
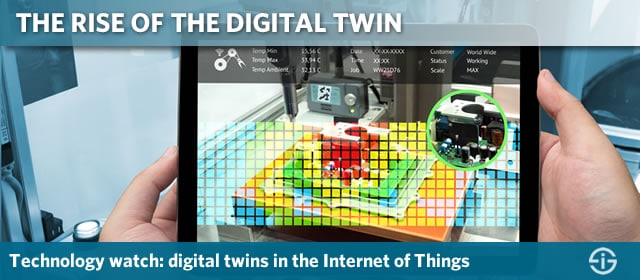
When you start hooking up IoT endpoints, devices and physical assets to data sensing and gathering systems which are turned into insights and ultimately into optimized/automated processes and business outcomes, as we do with the Industrial Internet of Things (among other things), there are quite some new possibilities that arise, to say the least.
A digital twin is a living model that drives a business outcome (Colin J. Parris, GE)
Even if we’re only really still seeing the tip of the possibility iceberg, sometimes it requires a bit of imagination to understand these opportunities. Digital twins are a perfect example of this and key in the Industry 4.0 vision and the Industrial Internet. Digital twins are definitely poised to deliver upon their many promises in manufacturing and beyond. A clear token of that is the growing support of digital twin use cases in Industrial IoT platforms.
We all have grown used to the concept and practice of digitization: books turned into e-books, paper information turned into electronic formats and digital processes, music in bits and bytes, the list goes on. We start to understand the opposite as well, for instance with 3D-printing. Digital twins are again something different. They are digital (software) copies of a physical asset. That’s the really simple definition. Let’s take a deeper look.
The digital twin: twice the fun, more than double the possibilities
For starters, let’s go back to our example of digitizing paper information, also known as document capture and scanning.
Once the full document or, more importantly the information we need from the paper document is scanned and archived or used to drive whatever business process, we can do two things with the original paper: get rid of it or keep it, for instance for regulatory reasons.
If we trash it, the paper-free dream, it’s gone and all we have is that digital information. No copy. With a digital twin, as the name indicates, we have two versions of a ‘thing’: the physical one and the digital twin one. In this case with a thing we don’t mean a paper document or a batch of paper to digitize but, you guessed it, the physical assets as we know them from the Internet of Things and, today, mainly the cyber-physical systems of the Industrial Internet and Industry 4.0, including the smart factory.
Digital twins are a dynamic software model of a physical thing or system (Gartner)
Imagine. You have an airplane engine with sensors and loads of sophisticated parts and technology as in the case of Rolls Royce which we mentioned in our Internet of Things examples.
What if you could make a fully virtual replica (not to be confounded with augmented reality but that’s coming as you’ll read below) in the cloud that is designed by engineers with CAD (computer-aided design) and CAD 3D models and “functions” as the real engine would do but then in a virtual form (simulation)?
If the virtual replica is really a digital twin and thus acts like the real thing, that would help us in detecting possible issues, test new settings, simulate all kinds of scenarios, analyze whatever needs to be analyzed, in fact, do pretty much everything we want in a virtual or digital environment, knowing that what we do with that digital twin also would happen when doing it with the ‘real’ physical asset. And that’s where we talk innovation and product design in entirely new ways too.
IoT feeds digital twins – who are hungry for real data
OK but how can we be sure that this would be the case? That’s where sensors and the Internet of Things, or better data, come in. The engine in our example or any other physical asset helps us in making our digital twin as it feeds data we need to make that digital twin a real twin.
Digital twins offer numerous benefits on which we’ll elaborate later. In fact, you might already have seen the concept in action. If you didn’t, the video below, using a bike equipped with sensors, gives you a good idea.
The current acceleration in the usage of digital twins is mainly possible thanks to IoT and the lowering costs of technologies that boosted both IoT and the digital twin
However, in real life you’ll notice that digital twins today are predominantly used in the Industrial Internet or Industrial Internet of Things and certainly engineering and manufacturing. If you remember our airplane engine or other complex and technology-intensive physical assets such as IoT-enabled industrial robots and far more, you can imagine why. You can even create a digital twin of a an environment with a set of physical assets, as long as you get those data.
That’s also why, when we speak about investments in and solutions for digital twins, we will typically encounter the names of companies that are very active in the Industrial Internet. GE, for instance. PTC, Siemens, CSC, SAP, the list goes on.
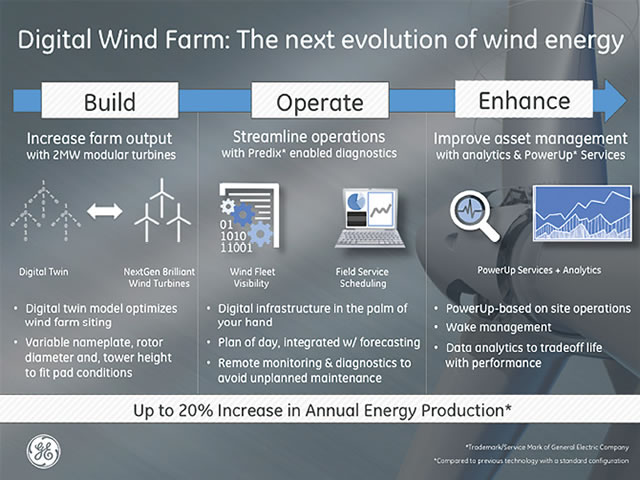
Three more things you might want to know about digital twins:
- The concept of digital twins isn’t THAT new. Here (PDF opens) is a whitepaper by Dr. Michael Grieves in which he explains ‘his’ digital twins concept in the scope of virtual factory replication, tracing back the roots of the digital twin concept to his University of Michigan Executive Course on Product Lifecycle Management (PLM) in days that most information was still paper-based and the information management and Manufacturing Execution Systems (MES) as we know them today didn’t exist yet (and of course there was no IoT).
- End 2016 Gartner put digital twins on its list of top 10 technology trends for 2017, and predicted that within three to five years from then ‘billions of things will be represented by digital twins, a dynamic software model of a physical thing or system’, which at the same time is how Gartner defines digital twins as you can read here.
- Digital twin technology also has roots in an entirely different context where you can get very far away from the machines you need to monitor and get repaired (monitoring and diagnostics is among the many reasons digital twins can be used for): space exploration As GE’s Dimitri Volkman wrote in a blog post in November 2016, the technology of pairing digital to physical objects was developed by NASA research back in the early days of space exploration whereby a digital model helped in operating, simulating and analyzing an underlying system governed by physics. You can imagine that the budgets, means and needs in space exploration were a bit higher than those of companies. NASA still uses digital twins but now also for similar reasons as in other ‘industries’.
The future of digital twins
In reality there are often several types of twins (for processes and for products, for instance).
You can also imagine that if many digital twins, which are all connected, get connected with each other as happens in the fleet of steam turbines in the video below (with similarity learning models), the overall insights and analytics become exponentially higher, leading to even more possibilities in complex operations.
In the future we’ll see twins expand to more applications, use cases and industries and get combined with more technologies such as speech capabilities, augmented reality for an immersive experience, AI capabilities, more technologies enabling us to look inside the digital twin removing the need to go and check the ‘real’ thing and so on.
Speaking about the future, analysts point at mainly 2020-2021 as the years where digital twins will be leveraged in key business applications (of course there are already plenty of examples and also in 2018 and 2019 digital twin technology is a hot topic).
Gartner sees the main place of digital twins in an IoT project context until give and take 2020. The company expects half of large industrial firms to use digital twins by 2021. However, more about the future of digital twins and these and other predictions via the button below.
Future of digital twins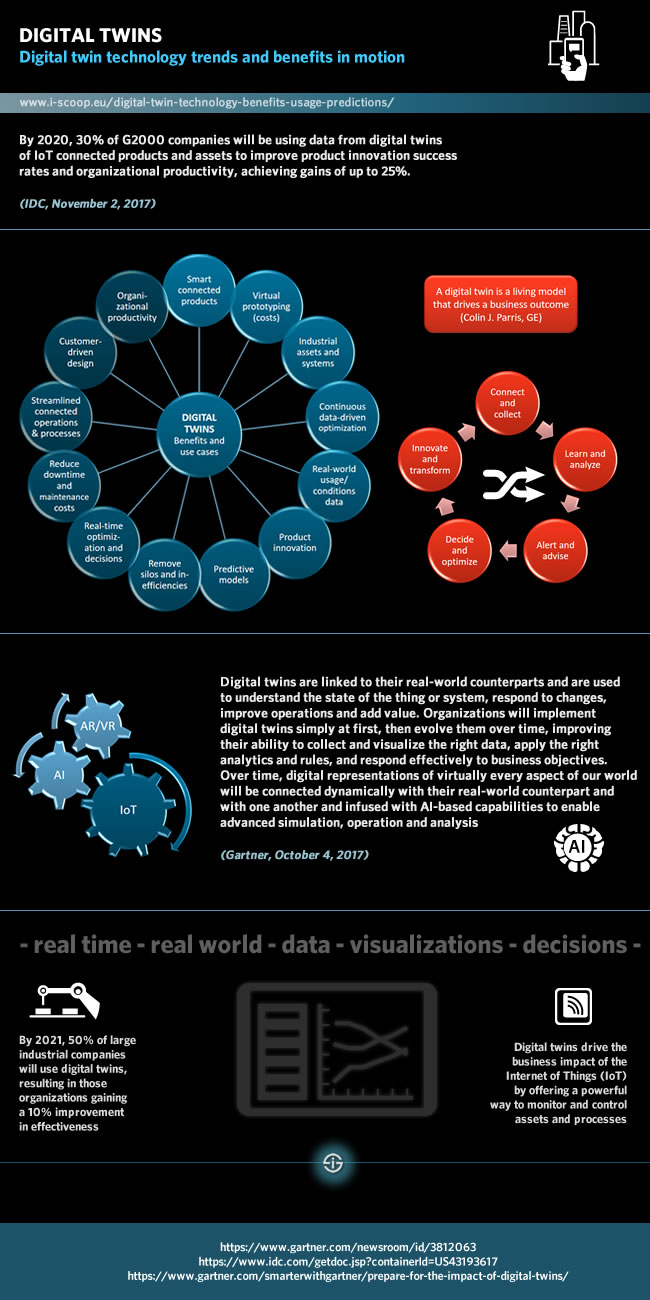
Digital twins made tangible: the bike example
At the edition 2015 of LiveWorx, the event of one the industrial IoT leaders, PTC, the company’s EVP CAD, Michael M. Campbell, explained the whole idea in easy terms, using the set-up PTC had constructed using a bike as you can see in the video on YouTube.
In a nutshell: the bike shows several technologies at work in the digital replication example. First the bike gets equipped with the necessary technologies and connected, making it ‘smart’ as we call that nowadays. The resulting information gets leveraged in a dashboard, in this case PTC’s ThingWorx of course, and then into that digital twin. The last step is leveraging the information in an augmented reality context.
Among the benefits: visibility into how the product is used in the real world and how it performs which in turn leads to goals such as product optimization, potentially insights for new products or versions, an improved and if feasible predictive service capability and so on.
In other words: data leveraged into intelligence into action in the crossing of digital and physical worlds. Of course, this is just a showcase video with some of the benefits in the scope of a specific product. You can imagine what happens if you have a digital twin of a wind turbine or a spacecraft to name just two. This doesn’t mean that the benefits (of which we only listed a few based on the video) or the products only concern big industrial assets and products. Just as the decreasing cost of technologies accelerated the evolutions in IoT – and thus in digital twin technology – in coming years the same decreasing costs and business cases in an ever smarter product environment will certainly expand to more and more products. And that might just happen sooner than we think.
Digital twins “living” models, driving business outcomes
In another video on YouTube, now from GE (after all they coined the term industrial Internet and do a lot in digital twins), Colin J. Parris, VP of Software Research at the GE Global Research Center takes you on a digital twin journey.
In the video Parris calls a digital twin a ‘living model that drives a business outcome’. That sounds far better than a digital, virtual copy of a physical asset indeed. And it’s of course far closer to the essence: the goals we want to achieve when using digital twins as of course there needs to be a rationale, a business case and a purpose of maintenance, optimization, cost savings or a mix of that and much more.
Although looking somewhat futuristic it’s a demo of an entirely different kind than the bike example and shows an actual steam turbine digital twin that immediately gives you a taste of how in digital twins the interface between man and machine through the digital twin and advanced technologies on levels such as AI and speech enable people – and soon other devices – to take actions based on a mix of data, from data on the edge (of IoT and edge computing indeed) and operational data to historical data. “See, think and do” as Parris calls it.
Top image: Shutterstock – Copyright: Zapp2Photo – All other images are the property of their respective mentioned owners.