An overview of the benefits, challenges and evolutions regarding remote monitoring, predictive maintenance, asset tracking, maintenance, management and optimization in Industry 4.0 and Industrial IoT.
Industrial markets are extremely asset-intensive. So, it’s logical that optimizing the utilization, management and tracking of assets is a key priority in Industry 4.0 with an increasing focus on predictive maintenance.
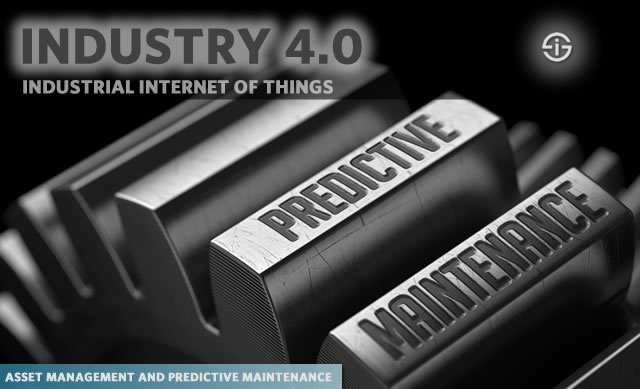
However, the market of solutions for advanced asset tracking, asset management, remote monitoring and remote/predictive maintenance is still facing several challenges as it is booming thanks to the Internet of Things (IoT) data analytics and artificial intelligence. Let’s take a look at some of the main challenges and, at the same time, opportunities.
It’s easy to see why asset management, asset tracking, predictive maintenance, remote monitoring of assets/conditions and, overall the optimization of everything with regards to assets, is so interesting for industries such as manufacturing but also logistics, facility management and smart building automation, oil and gas, and healthcare, to name a few.
Asset management, remote asset monitoring and maintenance: immediate benefits in a holistic and connected IIoT approach
By bringing in the Industrial Internet of Things for a connected asset ecosystem, along with the advanced solutions to monitor/visualize these assets, move to predictive analytics and act upon the resulting findings, a range of new possibilities opens up and immediate benefits can be gained.
Manufacturing and production, the original domain of the now broadened Industry 4.0 approach, in fact in a high degree is all about optimizing asset usage in an end-to-end way, certainly if we add people and even finished products to the broad range of inbound logistics, warehousing, production, transportation, plant floor and other asset environments as is typically done. With IIoT and advanced Asset Performance Management (APM), a holistic view and pro-active optimization becomes possible.
Efficiency through insights and analytics, including predictive, is a keyword here, across various levels.
Asset management, asset tracking and predictive maintenance: a matter of efficiency
The efficiency (and optimization) of assets today is mainly about production capacity and a real-time overview of the performance of equipment, a view on the production process and an identification of where moving assets (including people) and finished goods are with the goal of real-time adjustments in, for instance, scheduling, production planning and predictive maintenance.
Yet, also energy efficiency, communication efficiency, planning efficiency and maintenance efficiency, the very essence of predictive maintenance, are among the efficiencies sought. And at the end of the day there is also the goal of any digital transformation: efficient innovative solutions, based upon services which are driven by information efficiency and analytical learnings.
Yet, that requires to not just make asset management and tracking more efficient but most of all to look at existing ways of working, processes and asset utilization and insights in novel ways and from different angles – with data and analytics as differentiators.
Degrees of maturity: make downtime reduction and asset performance a first priority
Nevertheless, most industrial asset management and tracking today is still done from the perspective of efficiency, risk avoidance (reducing downtime), a bit of agility and only in limited cases true innovation.
However, moving from stage A to B and C in Industry 4.0 doesn’t happen overnight and there are quite some challenges with regards to asset tracking, management and monitoring, let alone gaining the insights for predictive maintenance, in earlier stages too.
Moreover, the capability to optimize the return of all types of assets through data collection, analysis, monitoring and action across several systems and workflows is already a daunting, yet highly valuable, task that results in clear gains.
Asset management, asset tracking and reducing downtime really should be a key priority, given the clear benefits and clear negative effects of downtime.
From an Internet of Things perspective one of the first challenges to address, when the business case is made, is how to include legacy assets and get data in an APM or other systems context from a hybrid environment with IoT-enabled assets, SCADA systems etc.
Benefits of smart asset management, remote monitoring of assets and connected maintenance at a glance
To summarize a bit, among the many benefits that can be realized by better leveraging assets in the connected factory, smart building and so on are:
- Increasing the performance of assets and production efficiency.
- Reducing asset downtime and asset failure, thus saving costs, including maintenance costs.
- Improving asset maintenance and developing new services around it.
- Increasing the utilization of assets from a time and resource allocation perspective.
- Moving towards an uninterrupted production process and better connected operational flows.
- Saving costs and enhancing ecological footprint by better gauging and controlling energy consumption and environmental conditions for energy conservation.
- Enhancing worker production, safety and operations in an increasingly information-intensive environment where man and machine collaboration (e.g. the evolution with regards to cobots) becomes more important.
- Gaining predictive analytics capabilities which enable to pro-act instead of re-act and provide a competitive and even potentially innovative differentiator.
- Enhancing supply chain planning and collaboration with ecosystem partners in an increasingly real-time environment.
- Increasing the return on investment and the economic return of all types of assets.
- Innovating and truly transforming existing processes and even revenue sources.
In the largest growing Industry 4.0 vertical, industrial equipment manufacturing, predictive maintenance will help the industry save up to 50% of maintenance cost by 2022.
The market of production asset management, asset tracking and advanced maintenance
Although spending in production asset management and predictive maintenance and field service isn’t as high as the number one manufacturing Internet of Things use case (manufacturing operations) according to IDC findings (January 2017) which we covered, predictive analytics and advanced maintenance services are certainly a leading cross-industry category from a project perspective.
After all, what better way to enhance customer satisfaction/loyalty/benefits and reduce costs at the same time than to make your installed base of industrial manufacturing products connected in order to optimize service, maintenance and plant floor efficiency?
Industrial equipment manufacturing leads the way
Soon the days that industrial assets needed to be serviced, depending on schedules and incidents with high human, service and maintenance costs, are over for all critical operations.
So, it shouldn’t come as a surprise that, as mentioned in our article on the spending evolutions in Industry 4.0 technologies, industrial equipment manufacturing will see the highest Compound Annual Growth Rate (CAGR) until 2022.
In the announcement of the May 2017 report which we tackled in that article, the main reasons for the rapidly growing implementation of Industry 4.0 technologies in that industrial equipment manufacturing industry was the avoidance of unplanned downtime and wastage.
Advanced asset tracking and production technologies: the growth drivers
April 2017 research from Frost & Sullivan states that Industry 4.0 is opening growth opportunities for advanced asset tracking and production technologies.
In the announcement, the research firm states that it expects that by 2021 various industries will have adopted asset tracking technologies in order to achieve their Industry 4.0 goals, enhanced workflow and smart manufacturing ambitions.
Among these sectors we find previously mentioned ones such a healthcare and logistics and a myriad of manufacturing and automation sectors in areas such as industrial automation, electronics, aerospace, military and fleet management.
The main reasons or this growing adoption of advanced asset tracking and production technologies according to Frost & Sullivan? Indeed: the prevention of asset failure, the improvement (and we would add economic return from a holistic perspective) of asset performance and lower downtime of assets such as machines.
Or as Frost & Sullivan analyst Jabez Mendelson puts it: “New asset management solutions will help manufacturers efficiently run the shop floor and ensure high standards in product lifecycle management across the supply and value chains.”
And those supply and value chains are exactly what Industry 4.0 is all about, starting from optimization and going to transformation and innovation by looking at them from different angles, enabling new business models, new services and new sources of revenue.
Hurdles to the adoption of asset monitoring and smart asset management
Among the challenges to tackle when looking to implement advanced asset tracking technologies (and asset maintenance technologies overall):
Standards, legacy assets and platform variety
Frost & Sullivan points out standards, since, as mentioned, asset tracking technologies indeed come in many flavors and combinations of several sub-technologies, device and solutions (also remember the legacy asset issue and the interoperability issues of IIoT and industrial protocols in general).
A lack of standards and different solutions and devices means more development and work and thus higher costs to implement and scale. This obviously goes for asset management and maintenance in an age of Industry 4.0 and the Industrial Internet of Things overall.
Moreover, it’s not as if suppliers of assets, from industrial robots to tooling technologies are sitting still either. They develop asset tracking, asset management and predictive maintenance solutions with predictive analytics for their (industrial) customers too (as an example: read how ABB Robotics developed a predictive maintenance service for its industrial customers). These systems, when in use at a particular company, need to be able to ‘talk’ with the overall asset performance management solution as well. Yet, depending on the vendors of tooling, machines, robots, warehouse assets and far more, these solutions are developed with different technological partners.
Security challenges in Industry 4.0 – asset tracking
Another challenge that Frost & Sullivan sees for the development of the advanced asset tracking technologies in Industry 4.0 is security, among others in relation with tracking devices and tags.
Yet, we rather see security as a clear and present concern to address holistically in Industry 4.0 overall, regardless of technologies. It’s not a surprise that several companies were showing new cybersecurity solutions for Industry 4.0 at Hannover Messe 2018.
Moreover, the challenge of security is different in your traditional IT environment than it is in industrial environments as you deal with IT, OT (Operational Technology), the increasing convergence of both, the complexity of the industrial environment with different protocols such as the SCADA protocols and then there is the Industrial Internet of Things and its connectivity aspects (whereby we see that – more recent – wireless IIoT connections are on the rise in the Industrial Internet of Things where most connections are fixed line as you can read here).
We’ve tackled (cyber)security in the Industrial Internet of Things previously and covered a report on industrial cybersecurity.
Frost & Sullivan points out that, from the perspective of advanced asset tracking technologies the various components, including smart tags and tracking devices can be sabotaged, hacked and obviously stolen.
In a holistic security approach, which is the only one that works, whether it’s in Industry 4.0 or any other area it’s important to include the human element (sabotage, theft, security in the physical world) and of course make sure you look at all the devices, technologies, communication protocols and so forth in order to avoid issues (and that goes for asset tracking too). Also take into account the sometimes hard conditions in which asset tracking devices need to operate, even on the human level with, for instance, personnel tags.
Jabez Mendelson on the challenges: “Technology developers are resolving these challenges by introducing advanced tracking and monitoring solutions with diagnostics capabilities”.
From preventive to predictive maintenance: work and disruption ahead
Let’s now take a look at predictive maintenance as such. According to MarketsAndMarkets, the overall predictive maintenance market is poised to grow from USD 1,404.3 Million in 2016 to USD 4,904.0 Million by 2021
In that growth the largest chunk is for manufacturing and it is expected that cloud-based predictive maintenance will grow faster. In the announcement you find more data.
Regardless of the precise data, what is most interesting though is the high Compound Annual Growth Rate (CAGR) of 28.4% until 2021. On the other hand, it’s not that surprising as costs are coming down (predictive maintenance condition monitoring solutions require technologies, solutions, skills and time). While traditionally it has been majorly seen as only being useful for the most critical operations there is a shift whereby less critical operations get included as everything gets more connected.
Obviously, this doesn’t mean that it suits all maintenance situations. Efficiency does also mean cost-efficiency. At the same time, however, it’s not just the costs and ROI from a spending and cost savings perspective that matters. As mentioned, Industry 4.0 is a journey whereby we also want to look at innovation and revenue potential, not just savings.
With increasing standardization, the overall lowering of the cost of the essential technologies to monitor, evolutions in the market of providers of solutions, the migration to a cloud model and an increasing usage of preventive maintenance in more markets, with industry equipment manufacturing at the front, expect more preventive maintenance and less preventive maintenance in a near future.
A main challenge for vendors of solutions will be to help customers solve the need for skills although the shifts in the needed skillsets in Industry 4.0 overall will certainly add to that too.
For now, and to conclude, let’s say that, as 2016 research by Infosys and FIR (the German Institute for Industrial Management) indicates, there is still work. While 87 percent of companies are aware of the potential of preventive maintenance with real-time data and analytics (note: preventive, not predictive, although it’s not preventive as you know it but de facto more predictive), only a small percentage implemented condition monitoring (15 percent) and the same goes for having incorporated machine status in the maintenance workflow (17 percent).
Yet, things might change fast as, if there is anything that lends itself to obvious benefits, service improvement and new ways of working it certainly is predictive analytics and preventive analytics based upon those real-time data and IIoT.
When concerns with regards to required skillsets, ease of use, ROI (and costs) and security drop the market will change fast. Moreover, with Industry 4.0 we are in highly competitive and disrupted environments whereby manufacturing is driven by the cascade effect of digital transformation and ever more demanding customers. In this landscape, when the cascade really starts getting felt and moves the needle from ‘urgent’ to ‘priority’, the leaders in embracing Industry 4.0 and predictive maintenance who reap the benefits of their investments will change the status quo for the laggards. And that can come with really high costs if you’re not ready as you are expected to by customers and everyone in your ecosystem and value chains.
From predictive maintenance analytics to analytics-based revenues
Before wrapping up a few words on maintenance analytics and predictive analytics. It’s clear that everything we described thus far in essence is about data, insights, analytics and resulting actions and services of assets that thus far have been limited in scope.
That’s where the Industrial Internet of Things in the end comes in. Not in the – indeed challenging – task of connecting assets but in defining which data and insights from which assets need to be tracked, combined, analyzed, monitored and leveraged in order to use these analytics in the most efficient way.
Prioritization as said is key here as it is in any digital transformation or Industry 4.0 journey. If an industrial asset such as an industrial robot goes down the cost effects can be pretty huge. Yet, it’s not just about looking at those kinds of assets.
What about analytics with regards to the condition of your perishable products when they are sitting in some container and the costs associated with them arriving in poor shape? What about the costs associated with factory workers who have to operate in sub-optimal circumstances? And, on the flip side, what benefits can you gain in terms of productivity by leveraging analytics and visualizing your entire asset and operations data as this mining case shows?
Predictive maintenance and maintenance analytics have been among the major focus points in Industry 4.0 and the Industrial Internet of Things as ABI Research already pointed out in 2014 when it predicted that maintenance analytics were expected to generate $24.7 Billion in 2019.
Now, just as back in 2014, the transformation of maintenance operations and reduction of downtime are first. The real questions for your next stages is what else can you do with this data and potentially other data in ways that allow you to generate revenue, innovate and build a competitive advantage or service capability that allows you to go beyond cost reduction and which the optimization of maintenance operations and downtime reductions in many cases essentially today is?
Asset data need to span the entire production life cycle
If you break down the various functions and processes in Industry 4.0 you really start seeing how important anything with regards to assets is: asset tracking, (predictive) asset maintenance and asset management overall.
It stretches across inbound logistics, actual production, warehouse management, product-related processes outbound logistics and transportation and obviously maintenance and services. In the RAMI 4.0 (Reference Architecture Model Industry 4.0) model’s life cycle and value stream dimension, it even needs to be included from the development stage on as the product data model starts with early data collection and data needs to be present for finished product and asset maintenance as well.
But before getting there, do make the case for the costs you can save and efficiencies you can gain by having a holistic asset management approach, leveraging IIoT for predictive maintenance. Just doing the math is often enough to get buy-in. And when you do the math (or ROI) don’t overlook costs which you might overlook such as insurance costs and more obvious costs you face today in any given asset-related perspective (with people and product as assets), which essentially means pretty much everything you do.
Top image: Shutterstock – Copyright: Tashatuvango – All other images are the property of their respective mentioned owners.