Over a decade after the official launch of the Industry 4.0 vision and its reference architecture models, there’s an increase in the number of ‘reality checks’: what have we achieved and what is holding us back? This article looks at a human and organizational aspect that over half of manufacturers encounter: the lack of skilled, connected factory workers to support digital transformation towards smart manufacturing.
Answering the many questions on why Industry 4.0 and its cyber-physical convergence hasn’t evolved faster isn’t a matter of just a few reasons. First, we need to agree on what Industry 4.0 essentially is. Then we need to understand what practice shows if we look at the prominent use cases and ‘progress’ across various industries, regions, and different “types” of organizations in an industry (differing in terms of ‘digital maturity’).
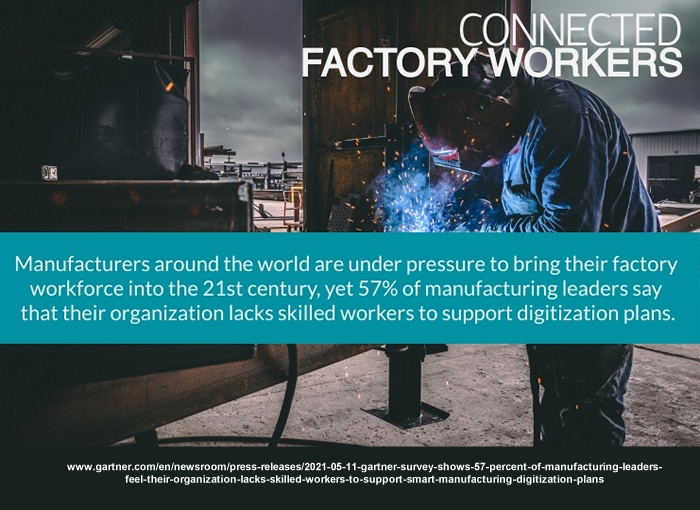
The more reality checks on the state, challenges, and even feasibility of Industry 4.0, the better. We can only repeat that in practice focusing on the goals and outcomes with a roadmap in mind is far more important than the marketing talk about ‘revolutionary’ technologies/solutions we had in the past decade.
Industry 4.0 has become a rather vague term, as tends to be the case with all ‘popular’ technology-related evolutions. But, more importantly, Industry 4.0 isn’t a matter of all those technologies and solutions such as cobots, IIoT, data analytics, AI/ML, digital twins, and so forth.
Industry 4.0 is mainly about a gradual secure, and smart manufacturing journey whereby people, management, partners, and connected factory workers must make that journey and underpinning strategy possible.
The vital role of connected factory workers
It requires connected factory workers who know what it means to bridge IT and OT in practice and dispose of the needed capabilities regarding digital savviness, having a data-driven culture, but also the knowledge, expertise, and creativity on top of these ‘new’ skills.
And it’s precisely here that many challenges remain. If you know the Industry 4.0 vision well, you probably know that the human and worker dimension has been somewhat overlooked in the original concepts presented by academics and engineers, looking at the road to a more autonomous cyber-physical world. It’s the reason why some started talking about Industry 5.0 some years ago: to put the ‘human’ back in the equation and/or center.
Yet, let’s not rush things and jump to the next buzzword (Industry 6.0 is talked about too already) before we know what the challenges are in the here and now.
“In the long term, it is important to establish a data-driven culture in manufacturing operations that is rooted in governance and training – without stifling employee creativity and ingenuity.”
To do so, in this article, we don’t look at Industry 4.0 from some industrial revolution aspect nor from the perspective technologies and solutions we’ve seen. And we agree to see the essence of Industry 4.0 or smart manufacturing as the evolution towards more integrated and intelligent systems whereby IoT and related technologies enable us to create value by bridging the ‘digital’ and ‘physical.’
To bridge that digital and physical world, you need people and processes. And people, the workers, have to bridge quite some things too, just as they have to acquire new – additional – skills to become connected factory workers. We know for a long time that IT (information technology) and OT (operational technology) aren’t the same worlds and have different technologies and people with quite differing views, cultures, habits, traditions, and capabilities.
Yet, that’s certainly not the only challenge and we talk about all workers who need to be connected. The thing is that in the end, in Industry 4.0, you’re in a digital and data-driven environment which comes with ample consequences. Moreover, realizing projects is one thing (and requires partners); getting the most out of them is another.
The lack of connected factory workers in consequences and perspective
Manufacturers today lack these connected factory workers with both the digital skills and tech-savviness on the one hand and the experience and knowledge.
Isn’t this a passing stage? Of course, it is to a large degree with, among others, Gen Z workers who are in the workforce and are acquiring the knowledge, experience, intuition, and so forth as they get to know the business and job better with each day that passes.
A second aspect we need to mention is the impact of the COVID-19 pandemic. As said earlier, not all manufacturing companies are the same. If we look at the manufacturing segments where the pandemic had the most impact, we see Consumer Packaged Goods (especially food and beverages) and Life Sciences. And, interestingly, these are two segments that so far lagged in terms of digital maturity and thus had to step up their game in the past year(s). It’s not a coincidence that CPG manufacturing companies are pushing investments in, among others, data and analytics services. Yet, they will also have to invest in the skills of their workers to make it happen.
An additional element that could change the ‘investment’ in programs to empower connected factory workers is governments’ investments in particular manufacturing areas (with Life Sciences being a perfect example). These programs often go hand in hand with educational support and initiatives to make groups of workers more used to work with digital, connected and data-driven tools.
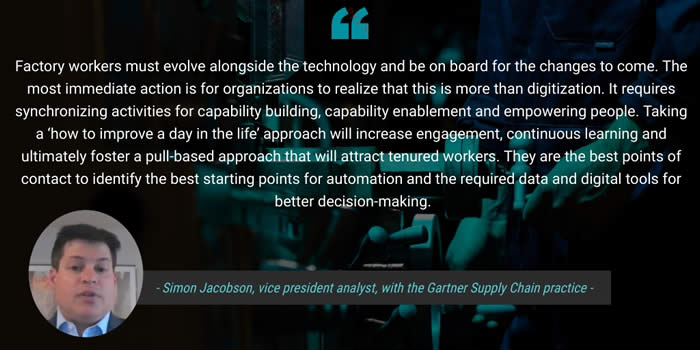
57 percent of manufacturing leaders feel they lack skilled workers to realize their goals: actions to take
Finally, it’s not just governments: with ever more ecosystems and platforms in particular industries where quite some training had to be done by prominent vendors during the pandemic, one can expect an influx of skilled workers in some areas too. There have been many industries where workers traditionally were less digital-savvy and hadn’t adopted digital tools, services and attitudes that much where training for some new kind of new (more digital) normal became important overnight.
Still, in the meantime, the challenge remains, and manufacturers can’t wait. According to a survey by Gartner, presented in May 2021, a whopping 57 percent of manufacturing leaders feel that their organizations lack the skilled workers that can support their smart manufacturing digitization plans.
For Gartner, manufacturers need a long-term strategy to develop the “connected factory worker”. In the meantime, they will keep going through a difficult phase of their digital transformation journey en route to smart manufacturing.
Simon Jacobson, vice president analyst, points to the two sets of skills the connected factory worker needs. While manufacturers “accept that changing from a break-fix mentality and culture to a data-driven workforce is a must, intuition, efficiency, and engagement cannot be sacrificed,” he says.
Jacobson states that new workers might be tech-savvy but lack access to best practices and know-how. Tenured workers, on the other hand, might have the knowledge but lack the digital skills. And a connected factory worker indeed needs both.
Connected factory workers need to leverage various digital tools and data management techniques to improve and integrate their interactions with physical and virtual surroundings while improving decision accuracy, proliferating knowledge, and lessening variability, per Gartner.
“Manufacturers are currently going through a difficult phase in their digitization journey toward smart manufacturing. They accept that changing from a break-fix mentality and culture to a data-driven workforce is a must. However, intuition, efficiency and engagement cannot be sacrificed. New workers might be tech-savvy but lack access to best practices and know-how — and tenured workers might have the knowledge, but not the digital skills. A truly connected factory worker in a smart manufacturing environment needs both.”
So, a matter of training? Partially. Alas, as per usual, the impact from a change management perspective is often underestimated.
Change management, including capability building, enablement/empowerment, teaching practical skills to do better, and continuous learning, isn’t just crucial to close the connected factory worker skills gap with existing workers but is also vital to attract the right talent.
Obviously, there’s more to it than that, and Gartner points out other elements needed to create connected factory workers and shares additional results from the survey that showed the gap here.
“Organizational complexity, integration and process reengineering are the most prevalent challenges for executing smart manufacturing initiatives. Combined, these challenges reflect the largest change management obstacles.”
Solving the several human challenges and the skilled, connected factory workers gap might be one of several ways to make your Industry 4.0 projects succeed or move to projects with clear goals and ROI, whereby people are equally essential.
Not that the lack of connected factory workers is the only problem we face after a decade, of course. There’s much more to come. Yet, without the right workers and skills, nothing works.
Gartner clients can read more in “Innovation Insight for the Connected Worker“.