There are a host of manufacturing buzzwords capturing modern trends. These include phrases such as “Internet of Things (IoT)” and “Industry 4.0”, “Big Data Analytics,” and so on. Among these new manufacturing catchwords, a related term has also emerged as a hot topic today: Predictive Maintenance (PdM).
The idea of predictive maintenance is to detect equipment issues before they become catastrophic. The process typically involves installing sensors on equipment that will detect problems early. The sensors feed information into a database or software package. Once a problem is found, maintenance is alerted and can work with the operations team to schedule a repair. This strategy helps avoid unplanned downtime and saves money for the operation.
It is evident why many manufacturers are interested in PdM programs. One PWC report found that 60% of operations with predictive maintenance programs realized uptime increases of 9% on average. Along with the uptime improvement, these companies saw cost reductions, asset lifetime extension, and risk reduction. Another report by teknowlogy Group (formerly CXP Group) found that predictive maintenance could reduce costs by up to 40%.
Of course, these benefits are appealing to many manufacturing operations – and they want to start their own maintenance down the predictive path. But what are the elements necessary for predictive maintenance?
There are certain prerequisites that an operation will need in place for a successful program. Read ahead to learn them.
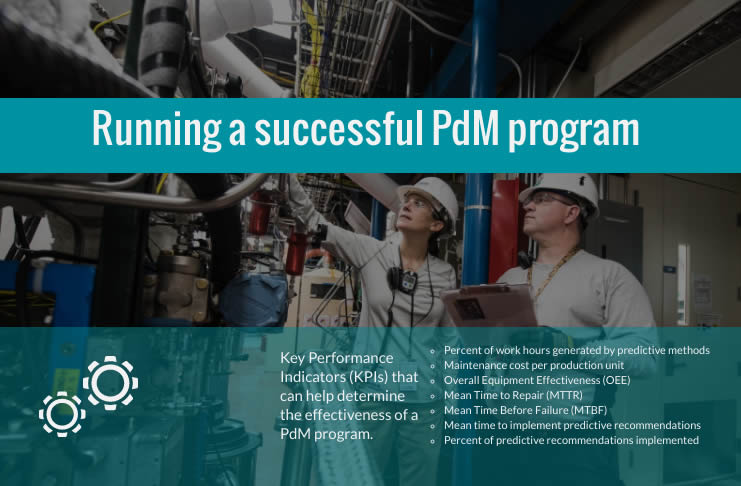
A PdM program requires top management support from the onset
The first prerequisite for a successful predictive maintenance program is backing and funding from top management.
After all, a PdM program will require adequate resourcing. This need manifests in funds allocated for hardware and software, as well as a commitment in man-hour resources for maintenance personnel.
Not only do the resources need to be allocated, but management should act as a champion – fostering the implementation and growth of the program. Without top management’s commitment, a PdM program will fail at the onset.
A clear understanding of the maintenance program
A PdM program should begin with a clear strategy in mind. This requires good insight into the existing maintenance situation.
PdM often begins as a pilot on one piece of equipment. The selection of equipment is important – it could be equipment that receives a lot of emergency maintenance, and/or has a few common fail points.
It is also critical to know the failure modes on that equipment. This helps ensure that the proper sensors are put in place, and the detection of the failures can occur before they become breakdowns.
Operations with PdM programs realize uptime increases, cost reductions, asset lifetime extension, and risk reduction.
Hardware and network prerequisites of a PdM program
Because a central tenet of PdM involves field sensors feeding information into a database, another prerequisite is the hardware.
This includes such devices as vibration sensors, temperature transmitters, pressure transmitters, ammeters, and more. There will need to be a way to find problems automatically, and hardware is the method.
Besides the sensors, there needs to be a way of transmitting the data to a central database. This is typically done through a wireless network – often an industrial network only used for machines and totally separate from a business network.
Note that a network need not be fully wireless to capture machine data. However, once deployed, a wireless network offers many advantages.
With a wireless network, sensors can be easily installed and commissioned. They can be moved quickly if needed, and adding additional sensors is a simple task. Costs are saved in future by avoiding expensive and time-consuming wiring work.
“Without top management’s commitment, a PdM program will fail at the onset” (Bryan Christiansen)
Software completes the puzzle – the value of a CMMS
Once you have the right machine sensor data feeding through a network, you need to do something with it. This is where software helps complete the puzzle of predictive maintenance. Sensor data is fed through the network to a central database, where it is presented to maintenance or operations for review.
There are many considerations with this step. Do you want a new software package to view, or one that integrates with existing platforms onsite? Who will view potential alerts – operations or maintenance? Or another department?
A CMMS is a valuable tool for this step, especially if you can integrate with PdM parameters. A CMMS can help you keep track of work orders, PdM alerts, failure modes, and more. The fewer systems that technicians must use, the better.
Training and change management
Implementing a predictive maintenance program is not a simple task from a personnel standpoint. All stakeholders need to be aware and involved. There will be changes to traditional maintenance practices, so another prerequisite for PdM program is training and change management.
Some strategies can help with change management. From the onset, involve technicians in the PdM process so that they feel invested. Communicate the purpose of the program and the potential benefits. Solicit their feedback on where to implement first – even if you don’t agree, consider taking their recommendations to earn their “buy-in.”
Performance tracking – KPIs to determine the success of the PdM program
After you have some sensors feeding into a software solution and are reacting to PdM alerts for some time, step back and assess the situation. Is the PdM program working effectively?
There are some advanced Key Performance Indicators (KPIs) that can help you determine the effectiveness of the PdM program. Here are some ideas:
- Percent of work hours generated by predictive methods
- Maintenance cost per production unit
- Overall Equipment Effectiveness (OEE)
- Mean Time to Repair (MTTR)
- Mean Time Before Failure (MTBF)
- Mean time to implement predictive recommendations
- Percent of predictive recommendations implemented
With a more comprehensive set of indicators in place, you can gain a good measure of the efficacy of your PdM program. You can also use these indicators to establish realistic targets for your PdM program. For example, double MTBF on an asset in 12 months.
Conclusion
If you are looking to improve your plant maintenance situation, predictive maintenance is a path to explore. Once you decide to go down that path, however, there are a set of prerequisites you should establish to ensure success.
These include management support, a good handle on your current maintenance issues, hardware, software, and training for your technicians. Without the proper fundamentals in place, your PdM program could fail before it starts. Taking the right steps at the outset of the program will help to ensure its future success.
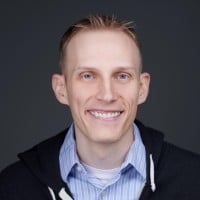
Guest blog by Bryan Christiansen
Bryan Christiansen is the founder and CEO at Limble CMMS. Limble is a modern, easy to use mobile CMMS software that takes the stress and chaos out of maintenance by helping managers organize, automate, and streamline their maintenance operations.