Additive manufacturing (AM) is increasingly used in the automotive industry. Why and how BMW Group uses 3D-printed components and intends to increase its use of AM.
In the automotive industry, new technologies are constantly tested and introduced. With changing consumers who want the latest technologies in their vehicles, technological innovation is a competitive differentiator for car brands. And of course, it’s not just about technologies in cars themselves and the driving experience.
Even if the customer experience is key in the digital transformation and innovation initiatives of car manufacturers, technological innovation is also high on the level of smart manufacturing, whereby, customer-facing purposes are part of the overall goals nonetheless.
Customization and personalization are often mentioned as drivers behind several Industry 4.0 technologies and initiatives for a reason. A good example is additive manufacturing. Thanks to 3D printing, you’ll be able to personalize your vehicle and selected components as a buyer in a not so distant future. In fact, several car manufacturers already took initiatives in this regard. One of them is the BMW Group that increasingly uses additive manufacturing.
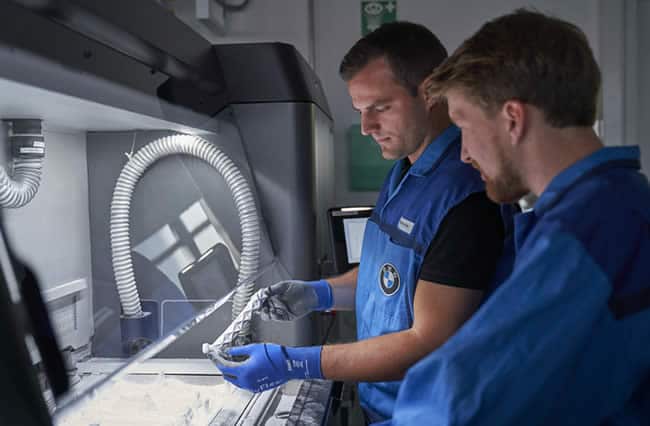
BMW Group: over 1 million 3D-printed components and counting – accelerating the use of additive manufacturing
At the end of 2018, the company announced it had produced more than a million parts over the last decade. Moreover, the use of 3D-printed components is accelerating at BMW Group.
The BMW Group Additive Manufacturing Center expects the output of components to reach over 200,000 components in one year, an increase of 42 percent compared to the year before.
Personalization isn’t the main reason why BMW Group increases the production of 3D-printed parts; efficiency and productivity reasons are. With so many components in cars, there is ample room to gradually move more parts to 3D printing, of course, especially with new methods being developed. Below are the ones the company emphasized at the occasion of its announcement regarding the increasing use of 3D-printed components with the mentioned milestone.
The company just celebrated the fact that it fitted its one-millionth 3D-printed component in series production: a window guide rail for the BMW i8 Roadster. It’s probably not a coincidence that BMW Group highlights this car. When IBM and BMW announced the launch of their so-called Watson IoT collaboratory in Munich, Germany, where the personalization of the driver experience is key, the BMW Group put four of its BMW i8 hybrid sports cars in IBM’s global HQ for Watson IoT. Yet, that was in 2016.
Back to the one-millionth 3D-printed part, a window guide rail, built in the car’s door to operate, well, the window, of course. It took the experts at the Additive Manufacturing Center of the BMW Group five days to develop the whole thing, and soon after, it was integrated into series production. It now continues to be used in series production with a production capacity of up to 100 window guide rails in 24 hours.
The window guide rail is also the second 3D-printed component inside the BMW i8 Roadster. The first one was the fixture for the soft-top attachment that is made of aluminum alloy and weighs less than the previously used injection-molded part, although, as a metal part, it’s stiffer. BMW Group received an award for it.
The near future of additive at BMW Group: personalization and series production
As said, additive manufacturing is also about to play an increasing role in the personalization of vehicles and their components, which is becoming ever more important and enabled by the new smart manufacturing techniques.
In 2016, when IBM and BMW announced their ‘collaboratory,’ IBM had released data from a study indicating that 54% of consumers want cars to learn about them to automate and personalize their driving experience. It won’t come as a surprise that car owners, certainly in specific demographics and for specific categories of vehicles, like to personalize the car as such too.
BMW Group already started testing these approaches with a site and platform to customize specific parts of MINI cars, using 3D printing technology. Although launched a while back, the website, an online shop really, of the – also awarded initiative – is still live, enabling eligible customers to chose from templates to, for instance, have their name on personalized side scuttles.
BMW Group started using additive manufacturing in 2010, initially for the production of smaller series of components. Other components for other vehicles followed, and it won’t stop there. Efficiency, costs, innovation, the customer experience, and, of course, branding are just some of the drivers for increasing AM initiatives in series production and for customization alike.
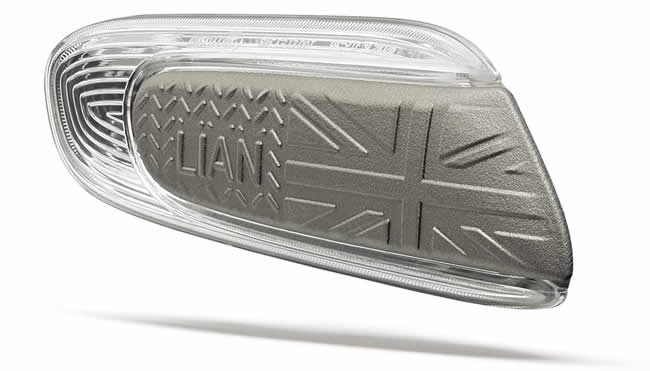
In the future, the goal is indeed to use additive manufacturing techniques for more series production.
However, for now, in discrete manufacturing, most use cases for additive manufacturing concern prototypes, aftermarket parts, and parts for new products. In the technology-intensive automotive industry where technological innovation is key in all (competitive) aspects, things just might go that tad bit faster.
For the window guide rail, BMW Group works with HP and uses HP Multi Jet Fusion Technology. Additive manufacturing will increasingly be used in mass production overall, certainly in automotive.
Another car company, VW, for instance, started using HP Metal Jet technology. The goal is to accelerate this at VW too, showing that bound metal additive manufacturing technologies are getting ready for mass production in the automotive industry.
All pictures ownership and courtesy BMW Group.