According to a SmarTech Analysis report, unveiled in December 2019, the market of bound metal additive manufacturing (AM) technologies will grow almost twice as fast as the overall metal AM market in the next ten years.
The bound metal AM technology market consists of two technologies: 1) metal binder jetting, and 2) bound metal deposition.
Through 2029, Smartech expects the overall metal AM hardware market to grow at an annual rate of close to 20 percent. Both metal printing AM segments are expected to do better with 30 percent for bound metal deposition and 35 percent for metal binder jetting technologies.
Bound metal AM technologies use special liquid and polymer binders to fuse metal powder into a green state geometric shape for subsequent sintering to achieve final properties (SmarTech Analysis)
Major players who have been investing in the development of bound metal AM technologies in the last three years include HP, GE Additive, Desktop Metal, Markforged and ExOne.
ExOne is a spin-off from manufacturing company Extrude Hone Corporation which exclusively licensed the metal binder jetting technology developed at MIT in in 1996.
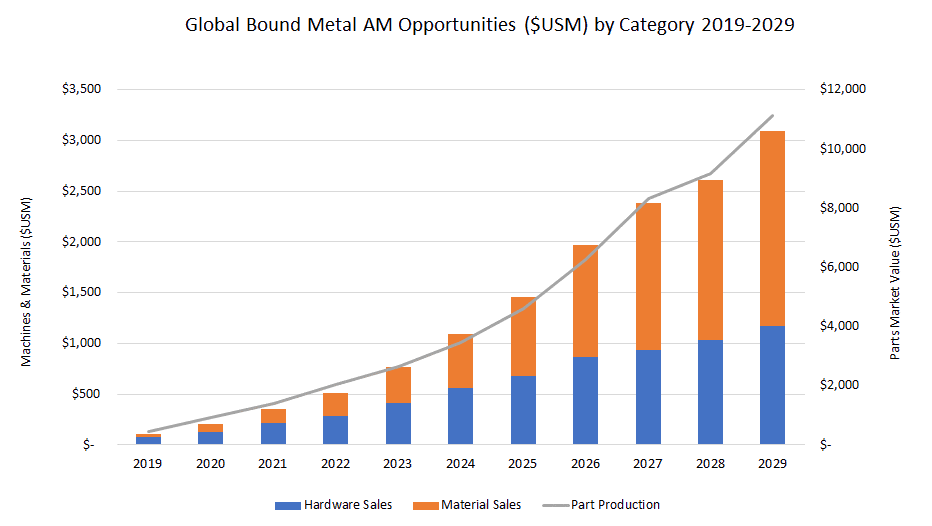
For several years, ExOne was the only company to provide metal binder jetting systems. Metal binder jetting technology now receives more attention again. The binder jetting process is well-suited for mass production applications in industrial and other applications, and some major companies intend to accelerate mass production with bound metal AM printers. An example is VW that works with HP’s new Metal Jet technology.
HP introduced this new HP Metal Jet technology at the end of 2018, promising to deliver mechanically functional final parts with up to 50x more productivity than other 3D printing methods and at a significantly lower cost compared to other binder jetting systems. The HP Metal Jet was positioned for mass production to ‘accelerate 4th industrial revolution’.
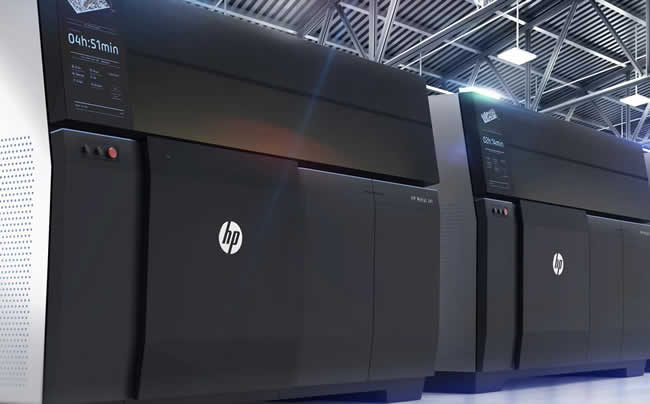
Talking about Industry 4.0: ExOne, a leader in industrial metal 3D printers and industrial sand 3D printers using binder jetting technology, strengthened its partnership with Siemens in the Summer of 2019. ExOne’s new S-Max Pro industrial sand printer includes the latest Siemens’ Digital Enterprise Portfolio of software and automation technology, including MindSphere, to leverage the benefits of Industry 4.0.
Whereas metal binder jetting technology obviously belongs to the family of binder jetting technologies, the second bound metal AM technology which SmarTech Analysis sees growing faster than the overall AM technology market, bound metal deposition or BMD is an extrusion-based metal AM technology, developed by Deskop Metal.
It powers Desktop Metal’s Studio System that enables rapid production of complex metal parts in-house. With Bound Metal Deposition, the 3D metal printer heats metal rods in cartridges, comparable to a plastic FDM (Fused Deposition Modeling) printer.
Bound metal AM technologies mainstream in metal additive manufacturing by 2023
Smartech also expects bound metal printing technologies to advance into the mainstream of metal AM by 2023.
- Metal binder jetting technology, the first of the two bound metal AM technologies, is expected to be initially closely linked to the MIM industry (metal injection molding) and adopted by companies that are familiar with MIM processing (see the X1 25PRO from ExOne as an example of a recent metal 3D binder jet machine with MIM powder).
- The second bound metal AM technology, bound metal deposition or BMD, could develop similarly as the polymer fused deposition modeling 3D printing technology, providing highly accessible metal additive capability with varying levels of performance and part properties, Smartech states.
According to the report, the primary material of choice will be steels, which are the most popular material in this early stage of bound metal AM technologies. This is partially due to the high level of sintering expertise for these parts and their cost-effectiveness, Smartech states.
Newer metal binder jetting machines are able to use Metal Injection Moulding (MIM) powders. These are significantly cheaper than metal powders developed specifically for 3D printing (AMFG)
While, for these reasons, steels are expected to be the primary material of choice, they will later be augmented by nickel alloys, titanium, and potentially aluminum.
Smartech reminds us that aluminum AM solutions are in high demand across technology segments, and players in bound metal technologies should benefit significantly if reliable aluminum printing and sintering solutions can be brought to market to compete with metal powder bed fusion.
With increasing investments and interest in bound metal printing, the industrial furnace industry will gain since a new sintering-based process becomes a focal point in the adoption of advanced manufacturing tech the analysts state.
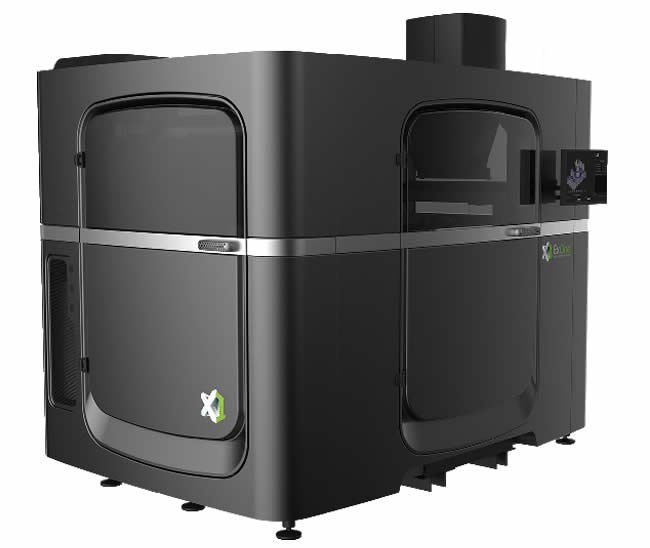
However, the differences and dynamics in the need and use of furnace technology in supporting the two very distinct bound metal printing technologies are likely to be significant.
SmarTech concludes that the implications for the ancillary equipment needed to support both processes are, unsurprisingly, quite different.
We have no commercial relationship with any of the mentioned companies. All images belong to their owners and are for illustration purposes.